That's pretty standard from what I've seen...but it is somewhat variable. Cumpiano says 15 degrees in his book.
Wow ok... must be a big differnce is small guage 6 string guitar strings vs larger guage bass strings - IDK...
Heres my stardard - its like 6 degrees and works well for cutting the neck laminates out of a full 8/4 eough cut boards. No scarf joint needed, they are full solid laminates.
I don't really even care if the laminates are aligned very well, after the glue dries i run the neck over the jointer to clean and sguare the face to the sides. Easy smezy -:lol
If i recall correctly i think this neck is 5 laminates.
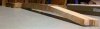
Last edited: