I'm building my first outfeed/assembly table for my workshop, this is the inspiration for the design:
https://www.reddit.com/r/woodworking/comments/7yzko8/my_new_outfeedassembly_table/
It will be a torsion box top created from mdf/ply/hardboard surrounded with a hardwood edge on all sides. I will also have a front vise installed in the same position.
Base will be simple 4x4 legs with stretchers/aprons and some yet to be determined configuration of storage underneath.
First question is this, I have some older "project" wood (oak) that is slightly over 4/4, can I get away with 1/2" thick edging for the sides? Keep in mind, the face of this edging will be the inner jaw of my front vise.
I'm asking this because I would like to resaw this board in half to get 2 sides from 1 board. From the pic above, it looks like 3/4", which I don't mind doing, but if I can get away with thinner, less waste.
Once that is done, what would be a good finish for this type of shop furniture, how best to protect the hardboard top and the hardwood edging?
Thanks for your time!
The lone pic of my torsion box assembly, I started off inline, but found that staggering was better in the long run.
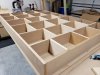
https://www.reddit.com/r/woodworking/comments/7yzko8/my_new_outfeedassembly_table/
It will be a torsion box top created from mdf/ply/hardboard surrounded with a hardwood edge on all sides. I will also have a front vise installed in the same position.
Base will be simple 4x4 legs with stretchers/aprons and some yet to be determined configuration of storage underneath.
First question is this, I have some older "project" wood (oak) that is slightly over 4/4, can I get away with 1/2" thick edging for the sides? Keep in mind, the face of this edging will be the inner jaw of my front vise.
I'm asking this because I would like to resaw this board in half to get 2 sides from 1 board. From the pic above, it looks like 3/4", which I don't mind doing, but if I can get away with thinner, less waste.
Once that is done, what would be a good finish for this type of shop furniture, how best to protect the hardboard top and the hardwood edging?
Thanks for your time!
The lone pic of my torsion box assembly, I started off inline, but found that staggering was better in the long run.
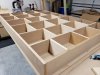