Look at this beauty I just picked up:
The top part weighs over 70 lb and the motor (1 hp Dayton) and stand feels even more!
I took it apart to clean and oil some parts but mainly to get at the knives:
I honed them until the stones glazed over (any hints on removing the glaze? I soaked them in mineral spirits overnight but to no avail). Then I planed a 3/4" pine board down to 5/8". Here are the shavings:
Do they look OK or do the knives need to be sent out for sharpening?
Never had a thickness planer before - it seems mighty hard to push that wood through - is that normal? I was only taking off 1/32" on each pass.
Cheers!
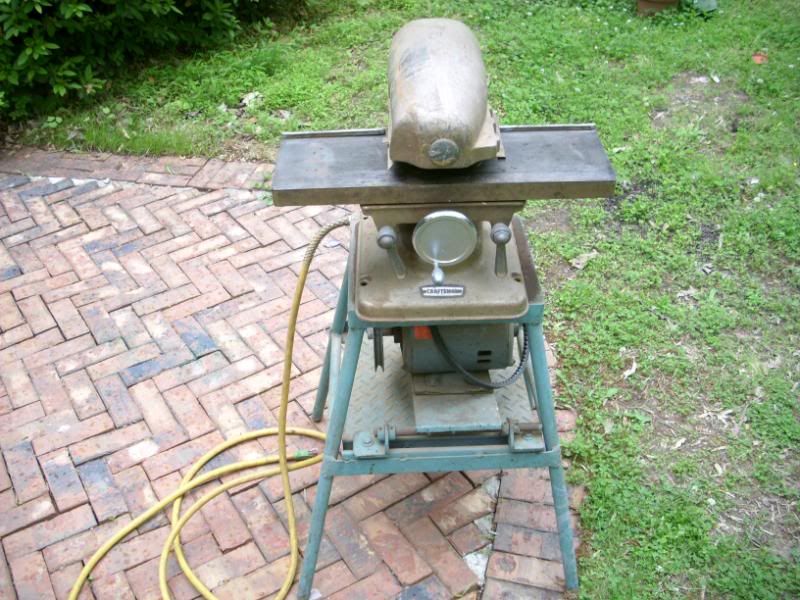
The top part weighs over 70 lb and the motor (1 hp Dayton) and stand feels even more!
I took it apart to clean and oil some parts but mainly to get at the knives:
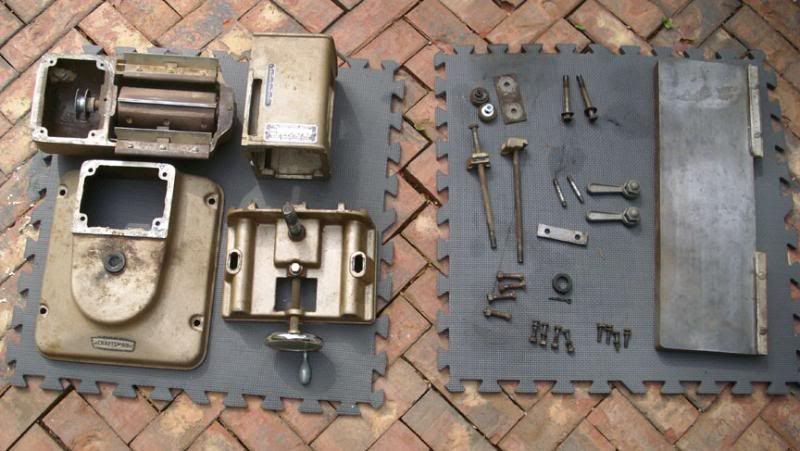
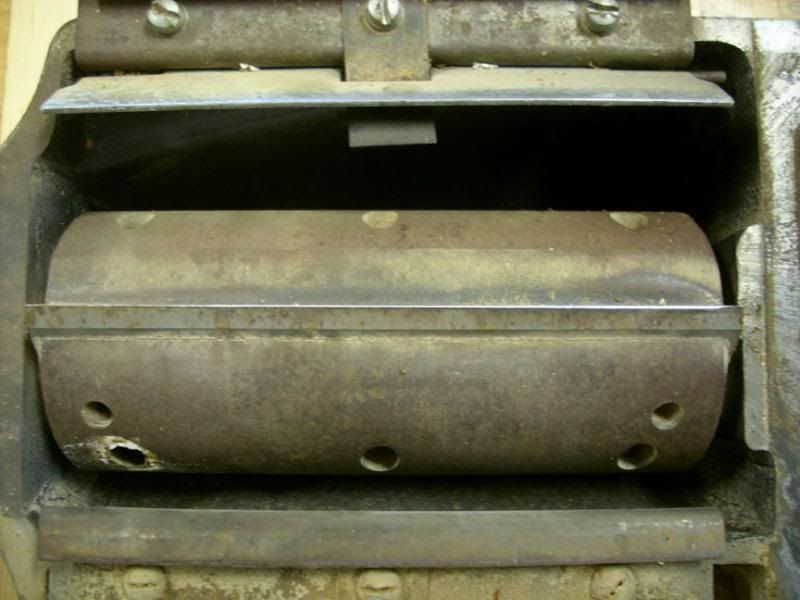
I honed them until the stones glazed over (any hints on removing the glaze? I soaked them in mineral spirits overnight but to no avail). Then I planed a 3/4" pine board down to 5/8". Here are the shavings:
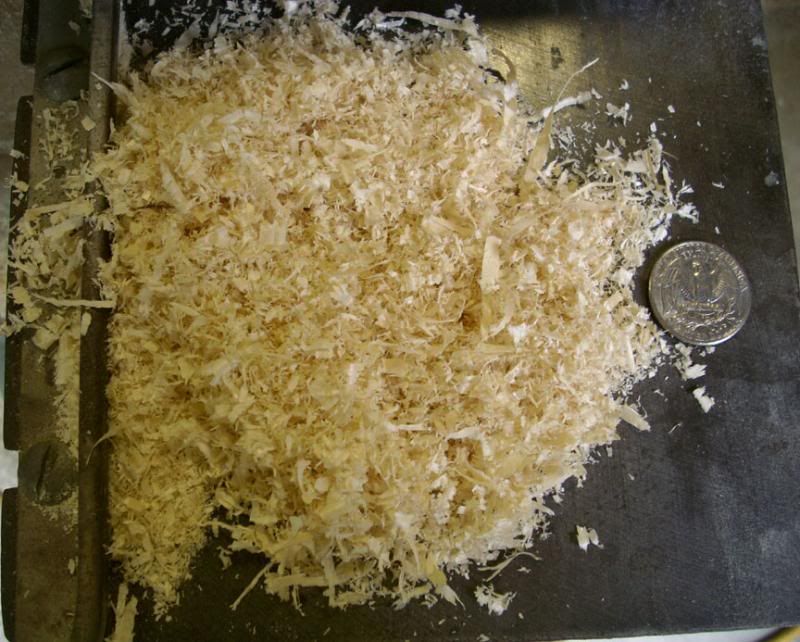
Do they look OK or do the knives need to be sent out for sharpening?
Never had a thickness planer before - it seems mighty hard to push that wood through - is that normal? I was only taking off 1/32" on each pass.
Cheers!