Saw this a while ago and was intrigued with the design. Found a set of plans over the Winter but wasn't able to get out in the shop to get started. As usual I can't let well enough alone so I'm modifying the original plans to suite me. Adding nuts and bolts head to pivot dowels and changing hot high intensity light for an LED I'll design and build from shop scraps left over from LED tail lights I made for Ethel a couple years ago. I'll need to design a power supply to use since I designed the tail lamps to use 12v dc car source. I'll post more as I go along... Got to adjust some of my time in the shop now because of more joint disintegration but GREAT to get back out making sawdust and splinters.
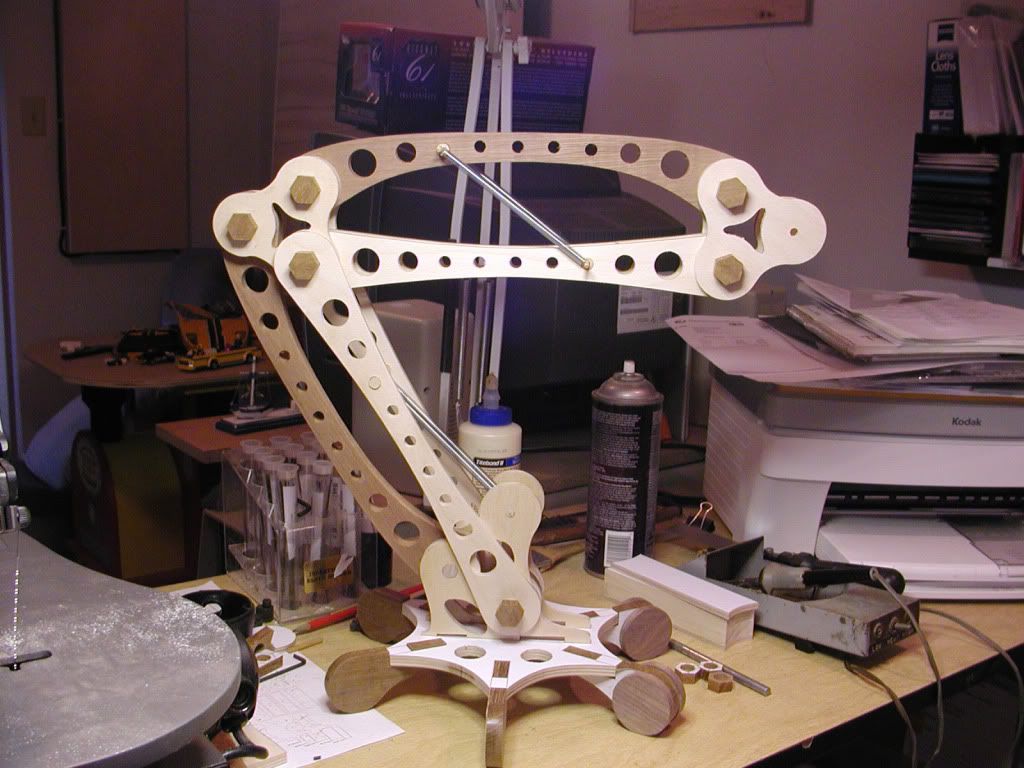
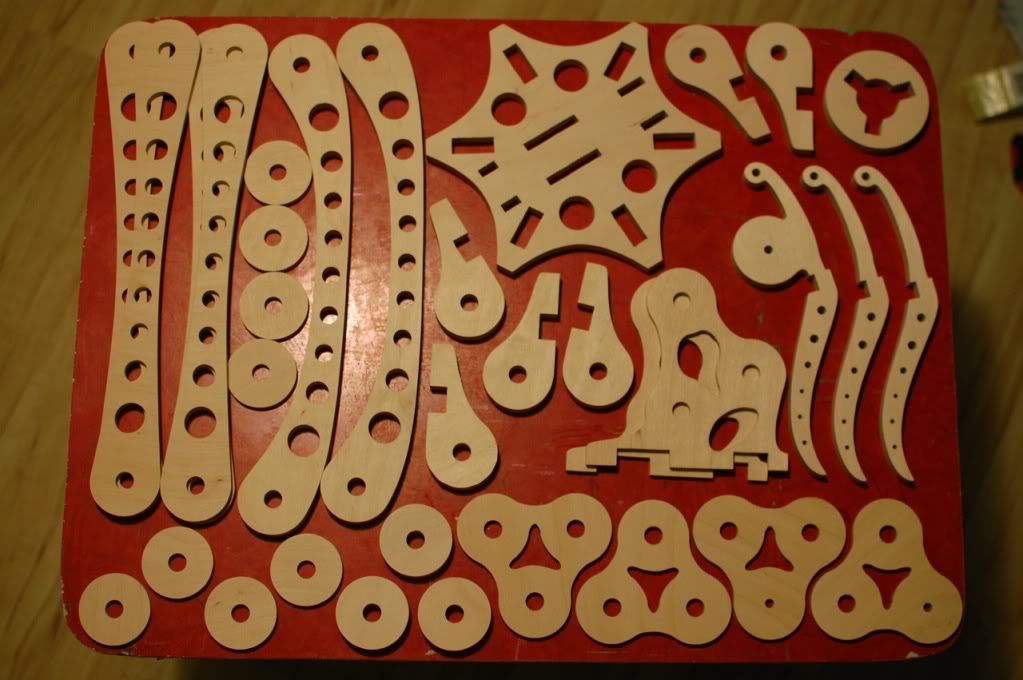
Last edited: