I got a big fiber barrel and made what I think is a pretty decent one after my first attempt collapsed a plastic trash can...
Here is the bucket with the top just sitting on it:
Here is the top:
Here it is with hoses hooked up about to test. That pile of saw dust is about 2' x 3' and maybe 4" deep, mostly very fine. I dumped the ShopVac out and beat the dust out of the filter and swept dust out of my 9" and 14" band saws because I had used both recently without DC.
Here is a close up of the pile:
I vacuumed it up through the separator in slow passes, but once I slipped up and went into the pile a little too heavy. I had read about that - it's a separator, so if you give it dust and no air, it can't separate. The first time I got this much in the vacuum:
So I tried again and was careful not to overload it. I got this:
A little more than nothing, but this was largely very fine stuff, so I am good with that. My guess is that is maybe 1% of the pile.
Here is where it lives now:
Here is the bucket with the top just sitting on it:
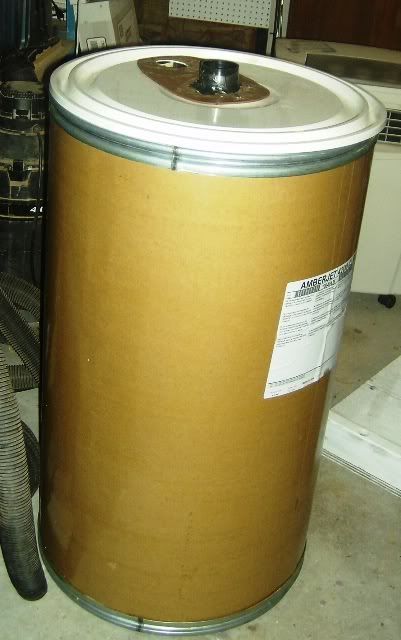
Here is the top:
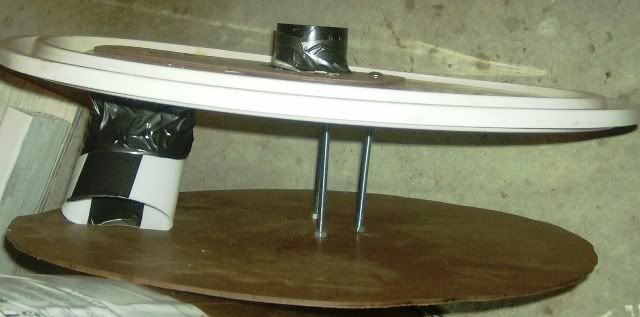
Here it is with hoses hooked up about to test. That pile of saw dust is about 2' x 3' and maybe 4" deep, mostly very fine. I dumped the ShopVac out and beat the dust out of the filter and swept dust out of my 9" and 14" band saws because I had used both recently without DC.
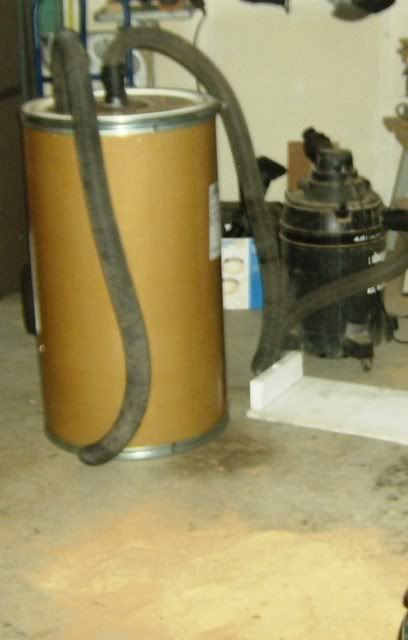
Here is a close up of the pile:
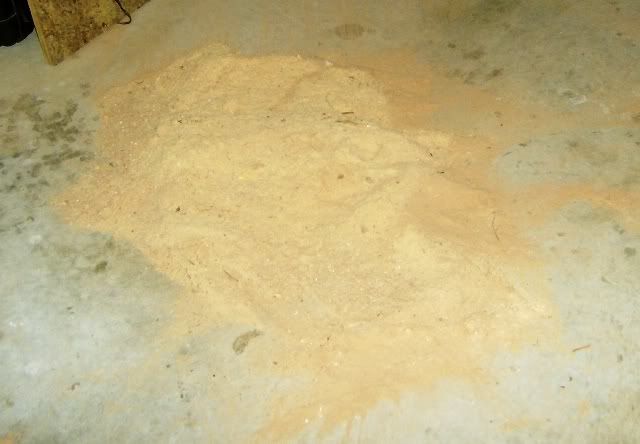
I vacuumed it up through the separator in slow passes, but once I slipped up and went into the pile a little too heavy. I had read about that - it's a separator, so if you give it dust and no air, it can't separate. The first time I got this much in the vacuum:
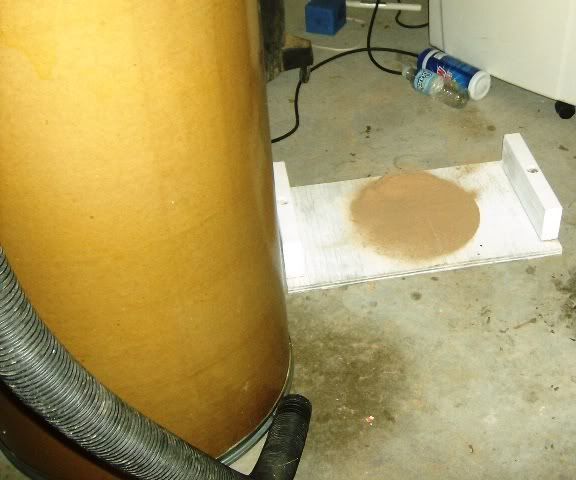
So I tried again and was careful not to overload it. I got this:
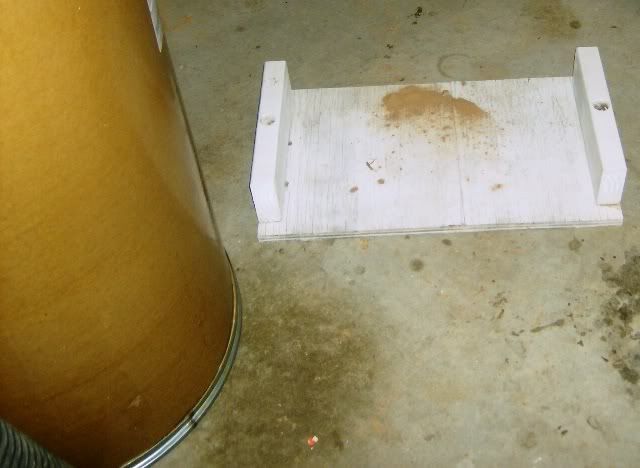
A little more than nothing, but this was largely very fine stuff, so I am good with that. My guess is that is maybe 1% of the pile.
Here is where it lives now:
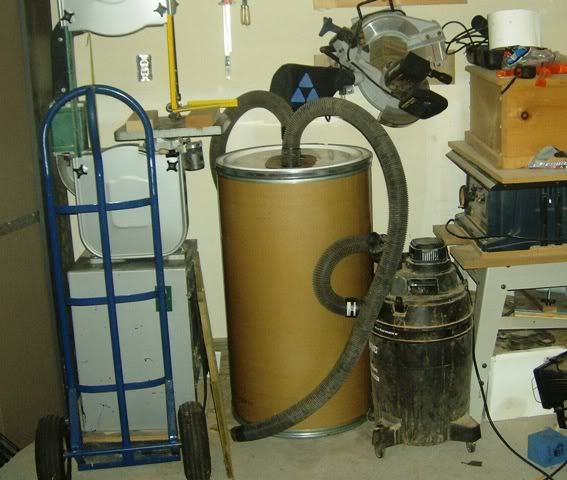