Fellas
I need some advice. I need to join narrower slabs to make tabletops. I am having trouble getting two edges true enough to clamp and glue.
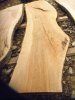
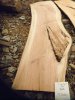
These will be 12in to 24in or so wide, 8/4 to 10/4 thick, and up to 16 ft long. Obviously I cannot run these across my joiner, too long and heavy.
So I have a couple of ideas to get an edge good enough to glue, and would like input from those of you with gluing
experience.
Idea #1 Festool 75 circular saw with guide, if anyone has one, I would love to bring a couple of slabs for a demonstration. I cannot buy one without knowing it will do what I need.
Idea#2 1/2 in arbor router ( and straight edge guide) with straight bit to clean up on uglier cut with my current skill saw. I think a smaller arbor bit would flex???
I plan to glue up these tops then plane and sand on my Lucas mill.
These are the two options I have come up with, and I am not even sure if either will work.
I am sure the right idea is somewhere in this forum base of knowledge.
Thanks so much.
Frank
I need some advice. I need to join narrower slabs to make tabletops. I am having trouble getting two edges true enough to clamp and glue.
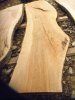
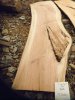
These will be 12in to 24in or so wide, 8/4 to 10/4 thick, and up to 16 ft long. Obviously I cannot run these across my joiner, too long and heavy.
So I have a couple of ideas to get an edge good enough to glue, and would like input from those of you with gluing
experience.
Idea #1 Festool 75 circular saw with guide, if anyone has one, I would love to bring a couple of slabs for a demonstration. I cannot buy one without knowing it will do what I need.
Idea#2 1/2 in arbor router ( and straight edge guide) with straight bit to clean up on uglier cut with my current skill saw. I think a smaller arbor bit would flex???
I plan to glue up these tops then plane and sand on my Lucas mill.
These are the two options I have come up with, and I am not even sure if either will work.
I am sure the right idea is somewhere in this forum base of knowledge.
Thanks so much.
Frank